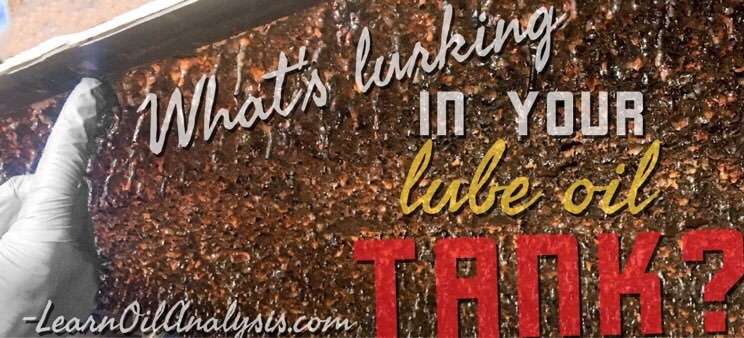
When we talk about condition monitoring especially with fluids and oils we tend to think about just the moving parts of the system. We think of the damage caused as components move against one another in a gear or bearing. We also think of dirt in the system causing scratches to component surfaces as it gets ground between two contacting surfaces. Yet we never seem to take much notice of the non-moving bits. Why is that? The lube tank just sits there but it is just as much affected by the condition of the fluid as any other component of the system.
The title headline picture of this article is taken from a hydraulic inspection hatch and the above picture is a scraping taken from that tank. When you look at the hatch it reminded me when as a student I went caving with some university friends and we saw really beautiful stalactites hanging from the ceiling of the cave. These are formed as water drips from the ceiling it deposits over time very tiny levels of dissolved minerals to form these protrusions of spikes shaped shards hanging from the ceiling over time.
Why did the tank lid of the lube oil tank have these stalactite like protrusions reminding me of the inside of a cave?
When we analysed the deposit the customer sent in it was almost entirely iron, more specifically rust. It appears over time condensation has built up on the lid causing rust and these dissolved iron particles have deposited the same as you see in caves on the tank lid. The strange thing was that the system was fairly new. It was only 2 and a half years old and it had been serviced at 12 months just before covid and the tank looked great. The next service was supposed to be serviced again in another 12 months months but was delayed until 18 months because of the pandemic and in 18 months this had occurred. The working environment was not even a very wet one and the system was stored inside, so this mean all this happened just with normal tank breathing and condensation in the air.
“The worrying thing was how this much rust had built up in just 18 months”
The tank bottom collects all the rubbish that builds up in the system such as rust, water, wear metals and varnish. These catalyse oxidation and if indeed they get circulated can cause wear in the system. In other cases they can cause false alarms when sampling if collected in error and also lead to overheating if oxidised varnish deposits collect on the tank wall.
Another example of a system with very dirty oil tank is below.
Not surprising the sample of oil looked pretty murky too…
A more recent example was from a Husky injection moulding machine. Anyone who knows these machine types will know these require NASA levels of cleanliness and have some of the strictest cleanliness requirements of any hydraulic systems in the world. As you can see there is a mass of metal that has collected at the bottom of the tank. It is worth noting the below image is taken with an iPhone, not a microscope so these are big bits up to a centimetre in size.
This actually reminded me of looking at the bottom of a wishing well.
So why does this all matter?
As stated previously the material at the bottom of the tank not only can cause wear should it be circulated, which may be obvious in stating. However, what is also not obvious is dirt, water, wear metals and in turn rust that collects at the bottom of the tank are actually a little reaction vessel at the bottom of the tank ageing your lubricant and causing varnish and overall lubricant deterioration. In fact today whilst writing this article we had a sample that had this very problem. The oil had a incredibly high varnish potential to the extent it formed a palpable black layer over the patch that very much reminded me of my leather wallet in texture. The graphic below is the actual patch as produced from the sample and is not adjusted for they graphic to make more leathery. The varnish when dried curled the patch and cracked to look like leather. This is what the inside of the customers tank system and components would likely look like if not addressed quickly. This material is a great insulator and deposits on nice cold tank surfaces, but is generated in hot conditions. If you follow the logic this means it will produce more and more insulation over time. This would eventually lead to huge overheating, component and valve sticking as well as machinery failure. All of this is because both the tank and the oil in the tank was not well maintained or monitored (this was the first sample the customer had ever done) despite the machine being 4 years old.
The wallet is also an apt example to compare to too as not only does the patch look like a leather wallet, but just like a varnish problem wallets are quickly emptied when condition based maintenance of lube oil systems and good maintenance practices are ignored.
If you are worried what is lurking in your lube oil tank, rather than have nightmares why not give your system a full health check with an oil and filter analysis. If you would like to find out more use the contact button on the bottom right of this page.